એનિલોક્સ રોલર કોષોનું અવરોધ ખરેખર એનિલોક્સ રોલર્સના ઉપયોગમાં સૌથી અનિવાર્ય વિષય છે,તેના અભિવ્યક્તિઓને બે કિસ્સાઓમાં વહેંચવામાં આવે છે: એનિલોક્સ રોલરની સપાટી અવરોધ (આકૃતિ.1) અને એનિલોક્સ રોલર કોષોનું અવરોધ (આકૃતિ. 2).
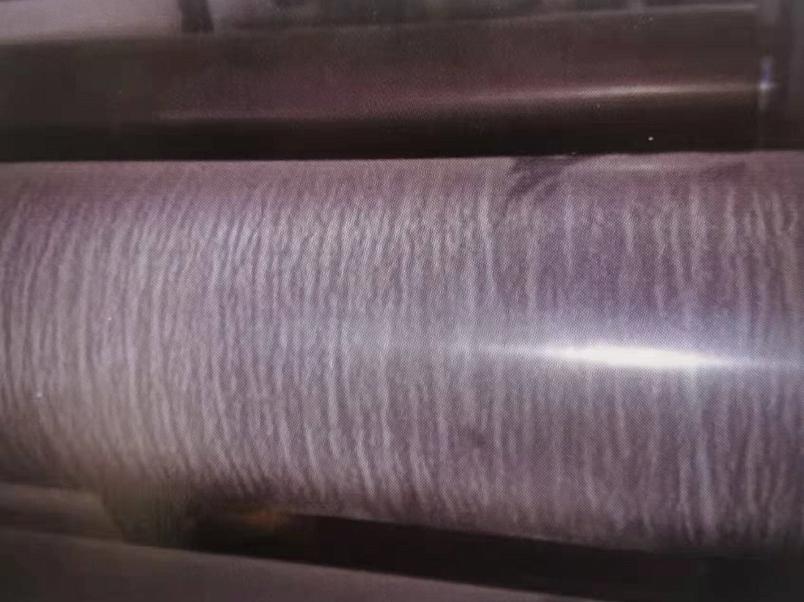
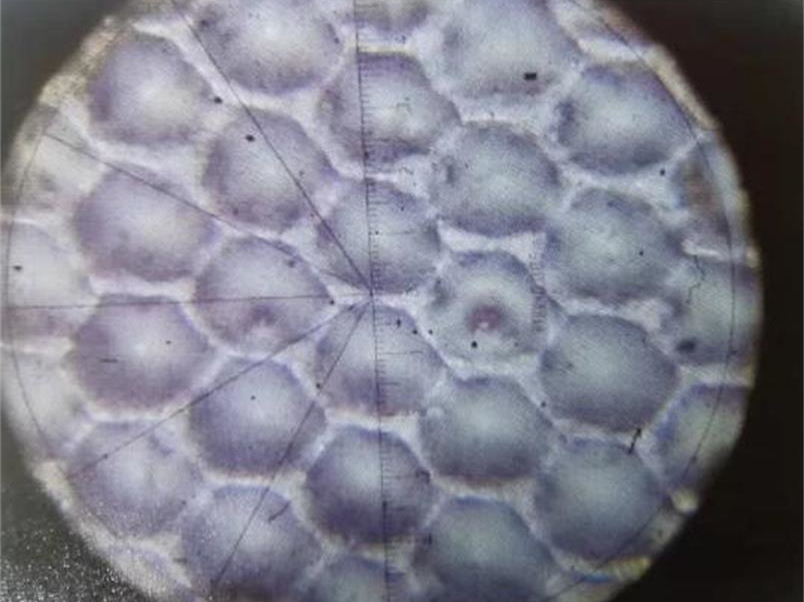
આકૃતિ .1
આકૃતિ .2
એક લાક્ષણિક ફ્લેક્સો શાહી સિસ્ટમમાં શાહી ચેમ્બર (બંધ શાહી ફીડ સિસ્ટમ), એનિલોક્સ રોલર, પ્લેટ સિલિન્ડર અને સબસ્ટ્રેટનો સમાવેશ થાય છે. ઉચ્ચ-ગુણવત્તાવાળા પ્રિન્ટ મેળવવા માટે શાહી ચેમ્બર, એનિલોક્સ રોલર કોષો, પ્રિન્ટિંગ પ્લેટ બિંદુઓની સપાટી અને સબસ્ટ્રેટની સપાટી વચ્ચે શાહીની સ્થિર ટ્રાન્સફર પ્રક્રિયા સ્થાપિત કરવી જરૂરી છે. આ શાહી ટ્રાન્સફર પાથમાં, એનિલોક્સ રોલથી પ્લેટ સપાટી પર શાહી ટ્રાન્સફર દર આશરે 40% છે, પ્લેટથી સબસ્ટ્રેટમાં શાહી ટ્રાન્સફર આશરે 50% છે. તે જોઈ શકાય છે કે આવા શાહી પાથ ટ્રાન્સફર એ એક સરળ ભૌતિક ટ્રાન્સફર નથી, પરંતુ શાહી ટ્રાન્સફર, શાહી સૂકવવા અને શાહી ફરીથી ઓગળવા સહિતની એક જટિલ પ્રક્રિયા છે; જેમ જેમ ફ્લેક્સો પ્રિન્ટિંગ મશીનની પ્રિન્ટિંગ ગતિ ઝડપી અને ઝડપી બની રહી છે, તેમ તેમ આ જટિલ પ્રક્રિયા માત્ર વધુને વધુ જટિલ બનશે નહીં, પરંતુ શાહી પાથ ટ્રાન્સમિશનમાં વધઘટની આવર્તન પણ ઝડપી અને ઝડપી બનશે; છિદ્રોના ભૌતિક ગુણધર્મો માટેની આવશ્યકતાઓ પણ વધુને વધુ ઊંચી થઈ રહી છે.
શાહીના સ્તરના સંલગ્નતા, ઘર્ષણ પ્રતિકાર, પાણી પ્રતિકાર અને રાસાયણિક પ્રતિકારને સુધારવા માટે, ક્રોસ-લિંકિંગ મિકેનિઝમ ધરાવતા પોલિમરનો ઉપયોગ શાહીમાં વ્યાપકપણે થાય છે, જેમ કે પોલીયુરેથીન, એક્રેલિક રેઝિન, વગેરે. કારણ કે એનિલોક્સ રોલર કોષોમાં શાહી ટ્રાન્સફર દર ફક્ત 40% છે, એટલે કે, કોષોમાં મોટાભાગની શાહી ખરેખર સમગ્ર છાપકામ પ્રક્રિયા દરમિયાન કોષોના તળિયે રહે છે. જો શાહીનો એક ભાગ બદલવામાં આવે તો પણ, કોષોમાં શાહી પૂર્ણ કરવાનું સરળ છે. રેઝિન ક્રોસ-લિંકિંગ સબસ્ટ્રેટની સપાટી પર કરવામાં આવે છે, જે એનિલોક્સ રોલના કોષોના અવરોધ તરફ દોરી જાય છે.
એ સમજવું સરળ છે કે એનિલોક્સ રોલરની સપાટી બ્લોક થઈ ગઈ છે. સામાન્ય રીતે, એનિલોક્સ રોલરનો અયોગ્ય રીતે ઉપયોગ કરવામાં આવે છે, જેથી શાહી ક્યોર્ડ થઈ જાય છે અને એનિલોક્સ રોલરની સપાટી પર ક્રોસ-લિંક થઈ જાય છે, જેના પરિણામે બ્લોકેજ થાય છે.
એનિલોક્સ રોલ ઉત્પાદકો માટે, સિરામિક કોટિંગ ટેકનોલોજીનું સંશોધન અને વિકાસ, લેસર એપ્લિકેશન ટેકનોલોજીમાં સુધારો અને એનિલોક્સ રોલ્સની કોતરણી પછી સિરામિક સપાટી સારવાર ટેકનોલોજીમાં સુધારો એનિલોક્સ રોલ કોષોના ભરાયેલાપણું ઘટાડી શકે છે. હાલમાં, સામાન્ય રીતે ઉપયોગમાં લેવાતી પદ્ધતિઓ જાળીની દિવાલની પહોળાઈ ઘટાડવા, જાળીની આંતરિક દિવાલની સરળતા સુધારવા અને સિરામિક કોટિંગની કોમ્પેક્ટનેસ સુધારવા માટે છે. .
પ્રિન્ટિંગ સાહસો માટે, શાહીની સૂકવણીની ગતિ, રિસોલ્યુબિલિટી અને સ્ક્વિજી પોઈન્ટથી પ્રિન્ટિંગ પોઈન્ટ સુધીનું અંતર પણ એનિલોક્સ રોલર સેલના અવરોધને ઘટાડવા માટે ગોઠવી શકાય છે.
કાટ લાગવો
કાટ એ એનિલોક્સ રોલરની સપાટી પર બિંદુ જેવા પ્રોટ્રુઝનની ઘટનાનો ઉલ્લેખ કરે છે, જેમ કે આકૃતિ 3 માં બતાવ્યા પ્રમાણે. સફાઈ એજન્ટ સિરામિક ગેપ સાથે નીચેના સ્તરમાં ઘૂસણખોરી કરે છે, નીચેના મેટલ બેઝ રોલરને કાટ કરે છે અને અંદરથી સિરામિક સ્તર તોડી નાખે છે, જેના કારણે એનિલોક્સ રોલરને નુકસાન થાય છે (આકૃતિ 4, આકૃતિ 5).
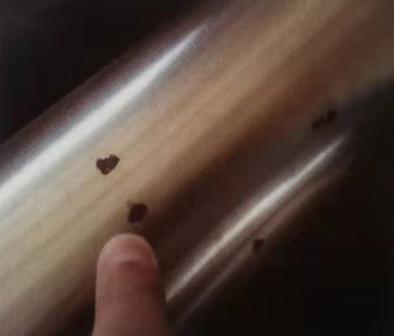
આકૃતિ 3
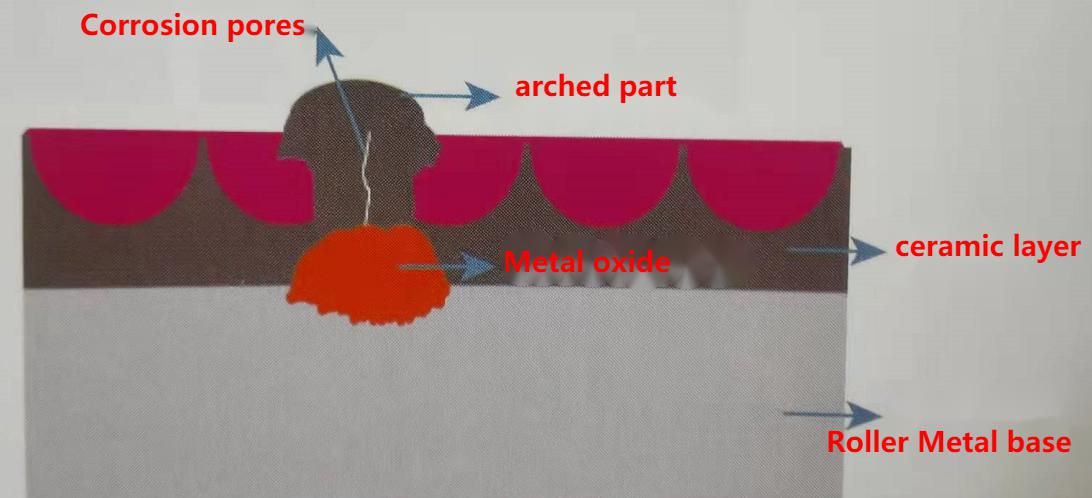
આકૃતિ 4
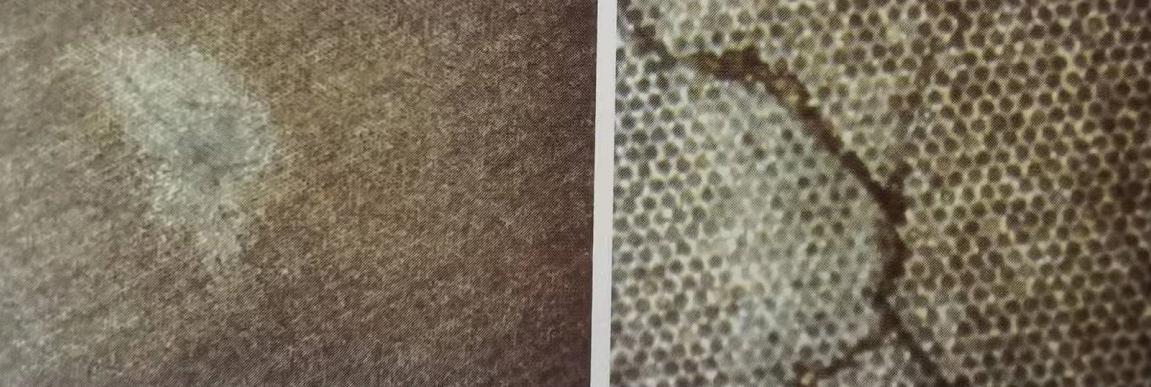
આકૃતિ 5 માઇક્રોસ્કોપ હેઠળ કાટ
કાટ લાગવાના કારણો નીચે મુજબ છે:
① કોટિંગના છિદ્રો મોટા હોય છે, અને પ્રવાહી છિદ્રો દ્વારા બેઝ રોલર સુધી પહોંચી શકે છે, જેના કારણે બેઝ રોલર કાટ લાગે છે.
② મજબૂત એસિડ અને મજબૂત આલ્કલી જેવા સફાઈ એજન્ટોનો લાંબા ગાળાનો ઉપયોગ, સમયસર સ્નાન કર્યા વિના અને ઉપયોગ પછી હવામાં સૂકવ્યા વિના.
③ સફાઈ પદ્ધતિ ખોટી છે, ખાસ કરીને લાંબા સમય સુધી સાધનોની સફાઈમાં.
④ સંગ્રહ પદ્ધતિ ખોટી છે, અને તે લાંબા સમય સુધી ભેજવાળા વાતાવરણમાં સંગ્રહિત થાય છે.
⑤ શાહી અથવા ઉમેરણોનું pH મૂલ્ય ખૂબ વધારે છે, ખાસ કરીને પાણી આધારિત શાહી.
⑥ ઇન્સ્ટોલેશન અને ડિસએસેમ્બલી પ્રક્રિયા દરમિયાન એનિલોક્સ રોલર પ્રભાવિત થાય છે, જેના પરિણામે સિરામિક લેયર ગેપમાં ફેરફાર થાય છે.
કાટ લાગવાની શરૂઆત અને એનિલોક્સ રોલને નુકસાન થવા વચ્ચે લાંબો સમય હોવાથી, પ્રારંભિક કામગીરી ઘણીવાર અવગણવામાં આવે છે. તેથી, સિરામિક એનિલોક્સ રોલરની બેગિંગ ઘટના શોધ્યા પછી, તમારે કમાનના કારણની તપાસ કરવા માટે સમયસર સિરામિક એનિલોક્સ રોલર સપ્લાયરનો સંપર્ક કરવો જોઈએ.
પરિઘ પરના સ્ક્રેચ
એનિલોક્સ રોલ્સના સ્ક્રેચ એ એનિલોક્સ રોલ્સના જીવનને અસર કરતી સૌથી સામાન્ય સમસ્યાઓ છે.(આકૃતિ 6)તેનું કારણ એ છે કે એનિલોક્સ રોલર અને ડોક્ટર બ્લેડ વચ્ચેના કણો, દબાણના પ્રભાવ હેઠળ, એનિલોક્સ રોલરની સપાટીના સિરામિક્સને તોડી નાખે છે, અને પ્રિન્ટિંગ રનિંગ દિશામાં બધી જાળીની દિવાલો ખોલીને ખાંચ બનાવે છે. પ્રિન્ટ પરનું પ્રદર્શન ઘાટા રેખાઓનો દેખાવ છે.
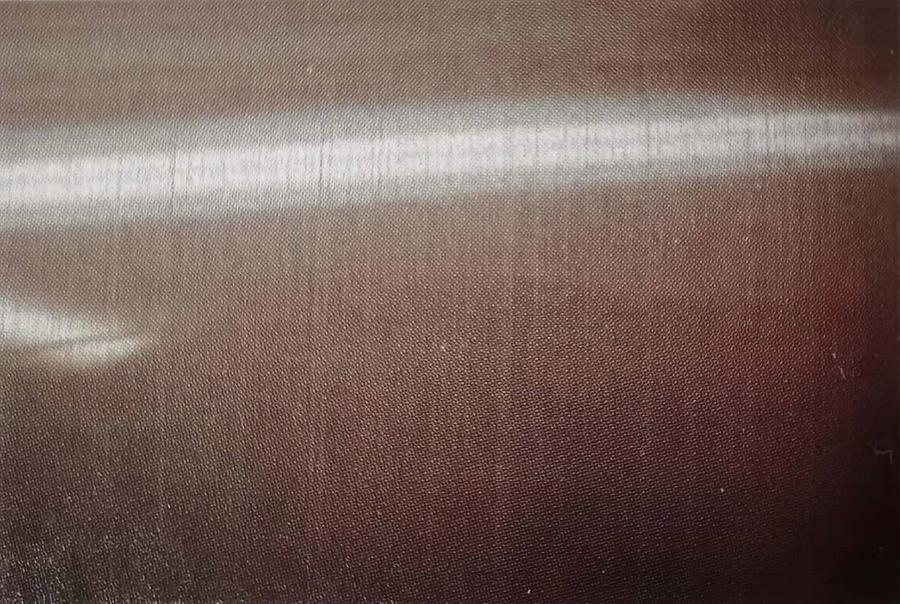
આકૃતિ 6 સ્ક્રેચ સાથે એનિલોક્સ રોલ
સ્ક્રેચની મુખ્ય સમસ્યા ડૉક્ટર બ્લેડ અને એનિલોક્સ રોલર વચ્ચેના દબાણમાં ફેરફાર છે, જેથી મૂળ સામ-સામેનું દબાણ સ્થાનિક બિંદુ-થી-મુખ્ય દબાણ બની જાય છે; અને ઉચ્ચ પ્રિન્ટિંગ ગતિ દબાણમાં તીવ્ર વધારો કરે છે, અને વિનાશક શક્તિ અદ્ભુત છે. (આકૃતિ 7)
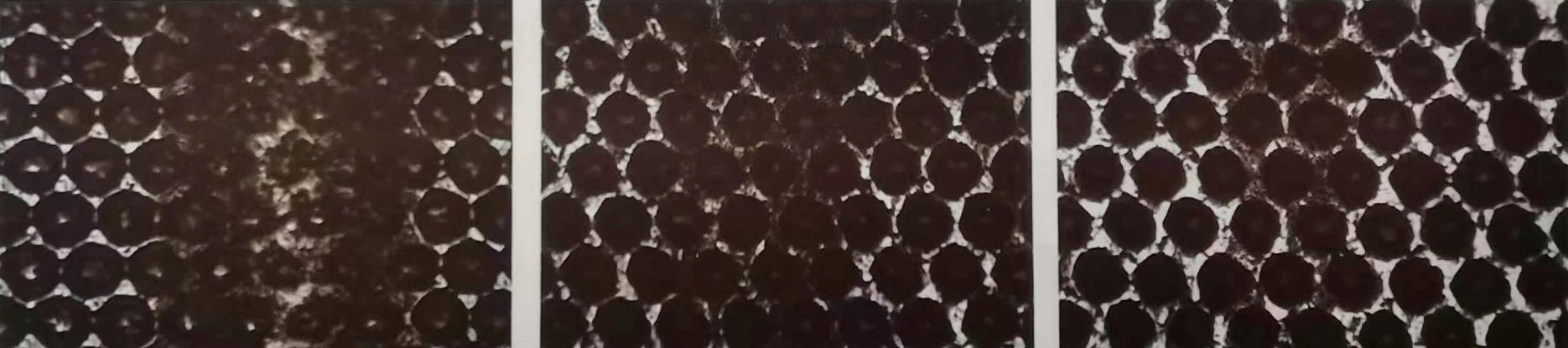
આકૃતિ 7 ગંભીર ખંજવાળ
સામાન્ય સ્ક્રેચ
નાના સ્ક્રેચ
સામાન્ય રીતે, પ્રિન્ટિંગની ગતિના આધારે, પ્રિન્ટિંગને અસર કરતા સ્ક્રેચ 3 થી 10 મિનિટમાં બનશે. આ દબાણમાં ફેરફાર કરતા ઘણા પરિબળો છે, મુખ્યત્વે ઘણા પાસાઓથી: એનિલોક્સ રોલર પોતે, ડૉક્ટર બ્લેડ સિસ્ટમની સફાઈ અને જાળવણી, ડૉક્ટર બ્લેડની ગુણવત્તા, ઇન્સ્ટોલેશન અને ઉપયોગ, અને સાધનોની ડિઝાઇન ખામીઓ.
૧. એનિલોક્સ રોલર પોતે
(1) કોતરણી પછી સિરામિક એનિલોક્સ રોલરની સપાટીની સારવાર પૂરતી નથી, અને સપાટી ખરબચડી છે અને સ્ક્રેપર અને સ્ક્રેપરના બ્લેડને ખંજવાળવામાં સરળ છે.
એનિલોક્સ રોલર સાથે સંપર્ક સપાટી બદલાઈ ગઈ છે, દબાણ વધી રહ્યું છે, દબાણ ગુણાકાર થઈ રહ્યું છે, અને હાઇ-સ્પીડ ઓપરેશનની સ્થિતિમાં જાળી તોડી રહી છે.
એમ્બોસ્ડ રોલરની સપાટી પર સ્ક્રેચ પડે છે.
(2) પોલિશિંગ અને બારીક ગ્રાઇન્ડીંગ પ્રક્રિયા દરમિયાન એક ઊંડી પોલિશિંગ લાઇન રચાય છે. આ પરિસ્થિતિ સામાન્ય રીતે જ્યારે એનિલોક્સ રોલ પહોંચાડવામાં આવે છે ત્યારે અસ્તિત્વમાં હોય છે, અને હળવા પોલિશ કરેલી લાઇન પ્રિન્ટિંગને અસર કરતી નથી. આ કિસ્સામાં, પ્રિન્ટિંગ ચકાસણી મશીન પર કરવાની જરૂર છે.
2. ડૉક્ટર બ્લેડ સિસ્ટમની સફાઈ અને જાળવણી
(૧) ચેમ્બર ડોક્ટર બ્લેડનું સ્તર સુધારેલ છે કે નહીં, ખરાબ સ્તરવાળા ચેમ્બર ડોક્ટર બ્લેડથી અસમાન દબાણ થશે. (આકૃતિ ૮)
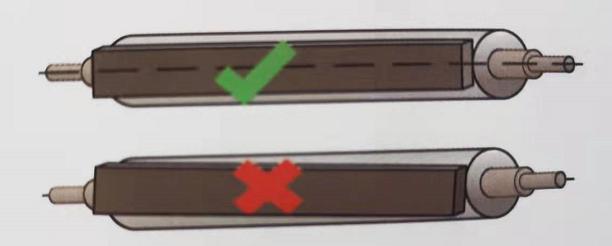
આકૃતિ 8
(૨) ડોક્ટર બ્લેડ ચેમ્બરને ઊભી રાખવામાં આવે કે નહીં, નોન-વર્ટીકલ ઇન્ક ચેમ્બર બ્લેડની સંપર્ક સપાટીને વધારશે. ગંભીરતાથી, તે એનિલોક્સ રોલરને સીધું નુકસાન પહોંચાડશે. આકૃતિ ૯
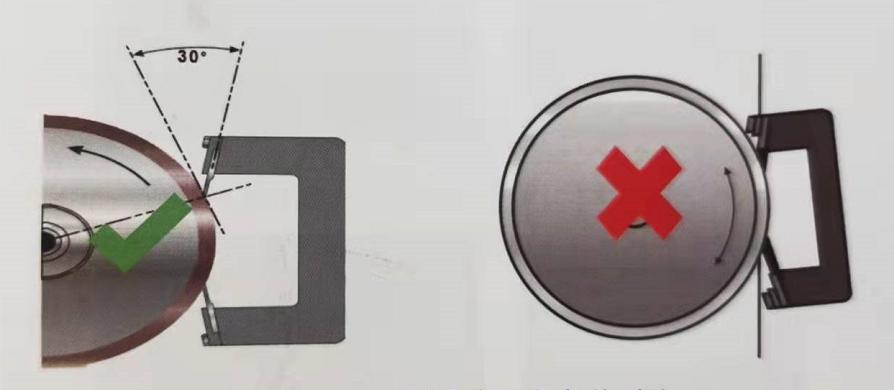
આકૃતિ 9
(૩) ચેમ્બર ડોક્ટર બ્લેડ સિસ્ટમની સફાઈ ખૂબ જ મહત્વપૂર્ણ છે, ડૉક્ટર બ્લેડ અને એનિલોક્સ રોલર વચ્ચે અટવાયેલી અશુદ્ધિઓને શાહી સિસ્ટમમાં પ્રવેશતા અટકાવો. જેના પરિણામે દબાણમાં ફેરફાર થાય છે. સૂકી શાહી પણ ખૂબ જ ખતરનાક છે.
૩. ડોક્ટર બ્લેડનું સ્થાપન અને ઉપયોગ
(1) ચેમ્બર ડોક્ટર બ્લેડને યોગ્ય રીતે ઇન્સ્ટોલ કરો જેથી ખાતરી થાય કે બ્લેડને નુકસાન ન થાય, બ્લેડ મોજા વગર સીધો હોય અને બ્લેડ ધારક સાથે સંપૂર્ણ રીતે જોડાયેલો હોય, જેમ કે
આકૃતિ 10 માં બતાવ્યા પ્રમાણે, ખાતરી કરો કે એનિલોક્સ રોલરની સપાટી પર દબાણ સમાન રહે.
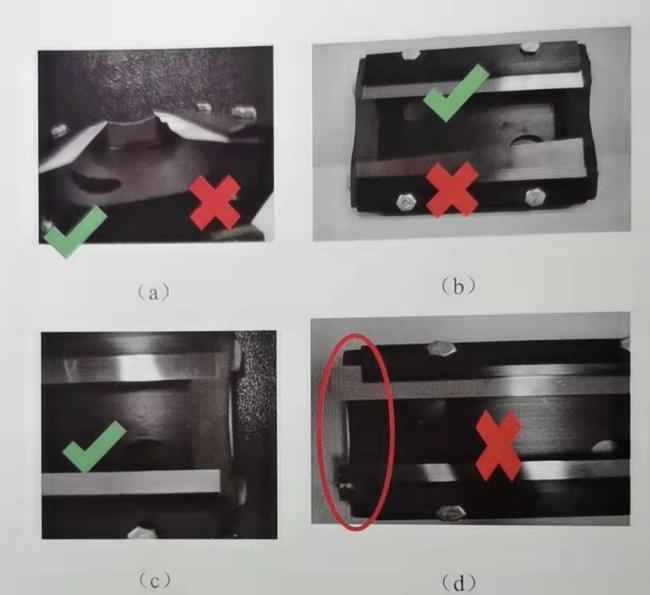
આકૃતિ 10
(2) ઉચ્ચ-ગુણવત્તાવાળા સ્ક્રેપર્સનો ઉપયોગ કરો. ઉચ્ચ-ગુણવત્તાવાળા સ્ક્રેપર સ્ટીલમાં ચુસ્ત પરમાણુ માળખું હોય છે, જેમ કે આકૃતિ 11 (a) માં બતાવ્યા પ્રમાણે, ઘસારો પછી કણો નાના અને એકસમાન હોય છે; ઓછી-ગુણવત્તાવાળા સ્ક્રેપર સ્ટીલનું પરમાણુ માળખું પૂરતું ચુસ્ત નથી, અને ઘસારો પછી કણો મોટા હોય છે, જેમ કે આકૃતિ 11 (b) માં બતાવ્યા પ્રમાણે.
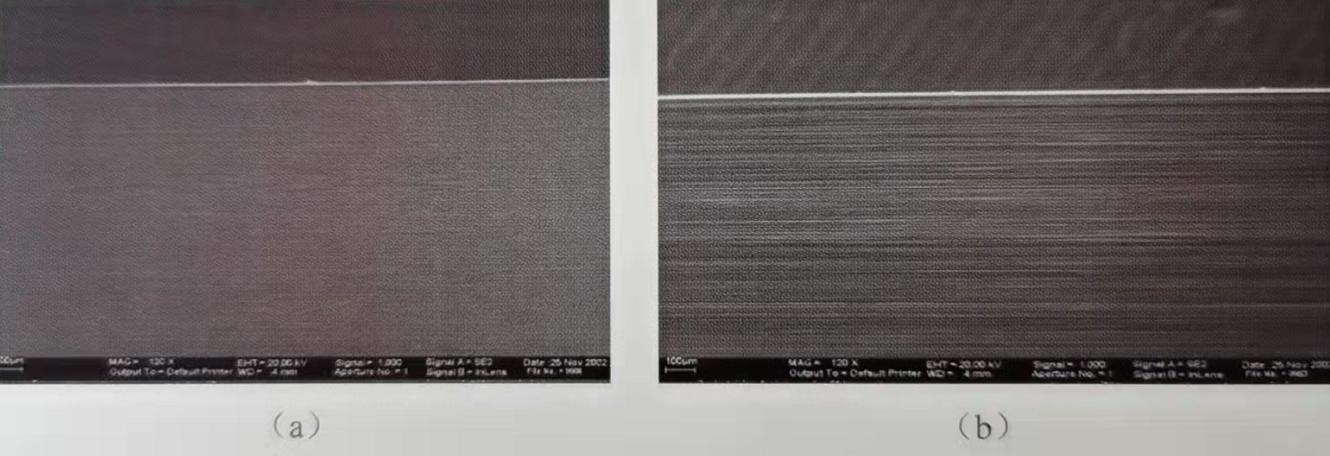
આકૃતિ 11
(૩) બ્લેડ નાઈફને સમયસર બદલો. બદલતી વખતે, છરીની ધારને ટક્કરથી બચાવવા માટે ધ્યાન આપો. એનિલોક્સ રોલરના અલગ લાઇન નંબર બદલતી વખતે, તમારે બ્લેડ નાઈફને બદલવું આવશ્યક છે. આકૃતિ ૧૨ માં બતાવ્યા પ્રમાણે, વિવિધ લાઇન નંબરો સાથે એનિલોક્સ રોલરની ઘસારાની ડિગ્રી અસંગત છે, ડાબી બાજુનું ચિત્ર નીચી લાઇન નંબર સ્ક્રીન છે બ્લેડ નાઈફ પર બ્લેડ નાઈફનું ગ્રાઇન્ડીંગ ક્ષતિગ્રસ્ત એન્ડ ફેસની સ્થિતિ, જમણી બાજુનું ચિત્ર હાઈ લાઇન કાઉન્ટ એનિલોક્સ રોલરના ઘસારાના એન્ડ ફેસની બ્લેડ નાઈફ સાથેની સ્થિતિ દર્શાવે છે. ડોક્ટર બ્લેડ અને એનિલોક્સ રોલર વચ્ચેની સંપર્ક સપાટી મેળ ખાતી ન હોય તેવા વસ્ત્રોના સ્તર સાથે બદલાય છે, જેના કારણે દબાણમાં ફેરફાર અને સ્ક્રેચ થાય છે.
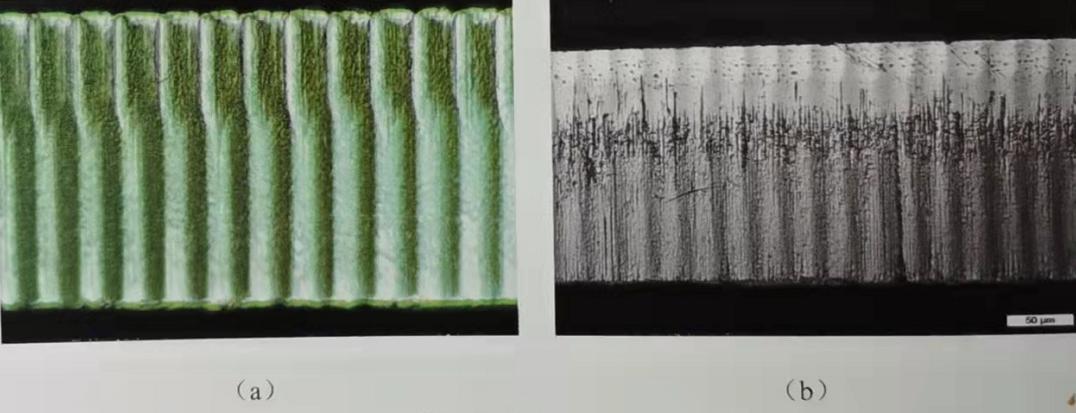
આકૃતિ 12
(૪) સ્ક્વીગીનું દબાણ હળવું હોવું જોઈએ, અને સ્ક્વીગીનું વધુ પડતું દબાણ સ્ક્વીગી અને એનિલોક્સ રોલરના સંપર્ક ક્ષેત્ર અને ખૂણાને બદલી નાખશે, જેમ કે આકૃતિ ૧૩ માં બતાવ્યા પ્રમાણે. અશુદ્ધિઓને અંદર ખેંચવી સરળ છે, અને દબાણ બદલ્યા પછી અંદર ખેંચાયેલી અશુદ્ધિઓ ખંજવાળનું કારણ બનશે. જ્યારે ગેરવાજબી દબાણનો ઉપયોગ કરવામાં આવે છે, ત્યારે બદલાયેલા સ્ક્રેપરના ક્રોસ સેક્શન પર ઘસાઈ ગયેલી ધાતુની પૂંછડીઓ હશે. આકૃતિ ૧૪. એકવાર તે પડી જાય, પછી તે સ્ક્રેપર અને એનિલોક્સ રોલર વચ્ચે ફસાઈ જાય છે, જેના કારણે એનિલોક્સ રોલર પર ખંજવાળ આવી શકે છે.
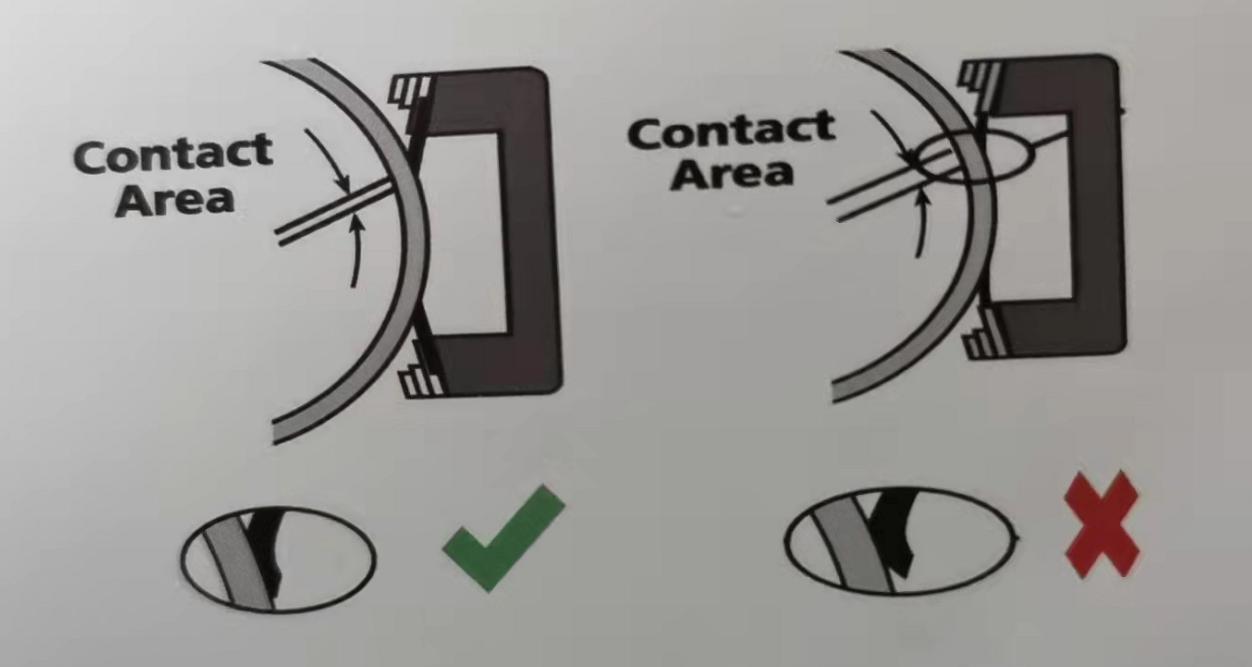
આકૃતિ ૧૩
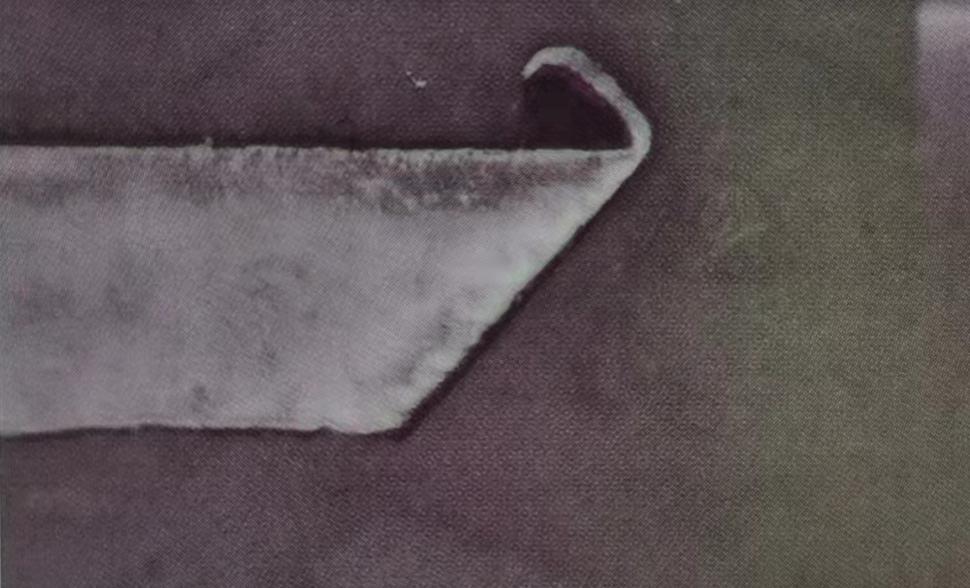
આકૃતિ 14
૪. સાધનોની ડિઝાઇન ખામીઓ
ડિઝાઇનમાં ખામીઓ પણ સરળતાથી સ્ક્રેચ થવાનું કારણ બની શકે છે, જેમ કે શાહી બ્લોકની ડિઝાઇન અને એનિલોક્સ રોલના વ્યાસ વચ્ચે મેળ ખાતો નથી. સ્ક્વિગી એંગલની ગેરવાજબી ડિઝાઇન, એનિલોક્સ રોલરના વ્યાસ અને લંબાઈ વચ્ચેની અસંગતતા, વગેરે, અનિશ્ચિત પરિબળો લાવશે. તે જોઈ શકાય છે કે એનિલોક્સ રોલની પરિઘ દિશામાં સ્ક્રેચની સમસ્યા ખૂબ જ જટિલ છે. દબાણમાં ફેરફાર, સમયસર સફાઈ અને જાળવણી, યોગ્ય સ્ક્રેપર પસંદ કરવા અને સારી અને વ્યવસ્થિત સંચાલન ટેવો પર ધ્યાન આપવાથી સ્ક્રેચની સમસ્યા ઘણી હદ સુધી ઓછી થઈ શકે છે.
અથડામણ
સિરામિક્સની કઠિનતા ઊંચી હોવા છતાં, તે બરડ સામગ્રી છે. બાહ્ય બળના પ્રભાવ હેઠળ, સિરામિક્સ સરળતાથી પડી જાય છે અને ખાડાઓ ઉત્પન્ન કરે છે (આકૃતિ 15). સામાન્ય રીતે, એનિલોક્સ રોલર્સ લોડ અને અનલોડ કરતી વખતે મુશ્કેલીઓ થાય છે, અથવા ધાતુના સાધનો રોલર સપાટી પરથી પડી જાય છે. પ્રિન્ટિંગ વાતાવરણને સ્વચ્છ રાખવાનો પ્રયાસ કરો, અને પ્રિન્ટિંગ પ્રેસની આસપાસ નાના ભાગોને સ્ટેક કરવાનું ટાળો, ખાસ કરીને શાહી ટ્રે અને એનિલોક્સ રોલરની નજીક. એનિલોક્સનું સારું કામ કરવાની ભલામણ કરવામાં આવે છે. નાની વસ્તુઓને એનિલોક્સ રોલર સાથે પડતા અને અથડાતા અટકાવવા માટે રોલરનું યોગ્ય રક્ષણ. એનિલોક્સ રોલરને લોડ અને અનલોડ કરતી વખતે, ઓપરેશન પહેલાં તેને લવચીક રક્ષણાત્મક કવરથી લપેટવાની ભલામણ કરવામાં આવે છે.
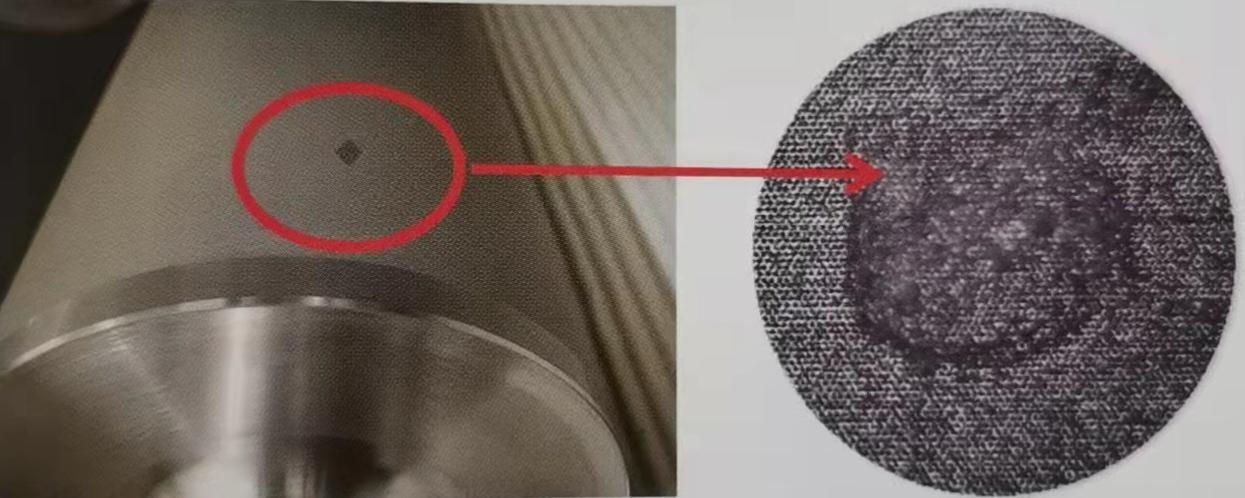
આકૃતિ 15
પોસ્ટ સમય: ફેબ્રુઆરી-૨૩-૨૦૨૨